Cold Weather Welding
A good weld is the result of skill, precision, access to quality equipment, and, ideally, favourable weather conditions. While hobby welders may have some flexibility in choosing when and where they weld, professionals often have to work regardless of the weather. Clients rely on them to deliver high-quality work even in the frigid grip of winter. Professional welding projects seldom halt due to cold weather, thanks to welders who know how to protect themselves, their equipment, and their materials from the elements. In this blog post, we’ll delve into the issues and solutions associated with welding in cold weather.
Keeping Yourself Warm & Comfortable
The first consideration when welding in cold weather is your attire. To weld safely, you must maintain feeling in your fingers, and you can’t afford to let the cold distract you. If you’re uncomfortable, the quality of your welds will suffer, so it’s essential to bundle up and wear practical clothing that doesn’t restrict your movement. Welding is a physically demanding process that requires concentration, and that can wane if you’re uncomfortably cold.
Safety is paramount when welding in winter, especially if you’re working at an elevated position. Ensure you use fall protection equipment and wear high-quality work boots with excellent traction to reduce the risk of slipping on icy scaffolding platforms. Regardless of what you wear to stay warm, make sure your outer layer is flame retardant, you’re sporting quality, heavy leather gloves (with a spare pair on hand in case yours get wet), and avoid wearing any polyester. As welding gas suppliers, we also offer a range of welding safety equipment suitable for cold weather welding.
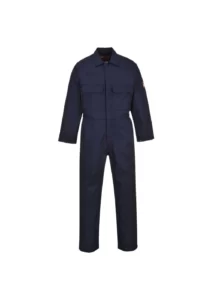
Keeping Your Equipment Safe
In winter, it’s crucial to consider the well-being of your welding equipment, especially when it’s in storage. Following gas cylinder storage rules—storing gas in a well-ventilated area, away from heat sources and combustible materials—should protect your MIG welding gas or TIG welding gas from the cold’s effects.
Your welding machine and rods require special attention in cold weather. Ideally, welding machines should be kept in a dry, moderately warm environment. However, manufacturers understand that this isn’t always feasible, so most good welding machines are designed to be heavy-duty and withstand temperature fluctuations. What you should be wary of is the dust and moisture that accompany cold weather. Excess moisture infiltrating your welding equipment can damage the machine and cause corrosion. Therefore, it’s advisable to cover your welder when not in use during winter to shield it from dust and moisture.
Industrial welding supplies like welding rods should also be stored in a warm, dry place and handled with care. If a welding rod becomes wet during use, the heat from the arc can cause the shielding layer of the rod to crack and crumble, leading to contamination of the weld and inadequate shielding of the weld puddle.
How Are Welding Materials Affected by Cold Weather?
Most metals become brittle at low temperatures, with a transition from ductile to brittle occurring within a specific temperature range. For many types of steel, this transition happens at 0°C, making welding in cold weather challenging. However, stainless steel has a much lower ductile-to-brittle transition temperature (around -200°C), allowing for safe welding in winter without the risk of shattering. Before welding in low temperatures, it’s crucial to check the specific ductile-to-brittle transition temperature of your chosen welding material.
Weld Strength in Cold Temperatures
The strength of a weld can be compromised by cold temperatures, resulting in cracking and poor penetration due to rapid cooling. Cold conditions cause welds to cool faster, and other factors such as steel chemistry, hydrogen levels in the weld, and humidity in the work environment can also impact weld strength and quality.
Preheating Metal Workpieces
To avoid base metals immediately absorbing heat from a fresh weld due to cold weather, which can lead to cracking and poor penetration, preheating the workpieces is recommended. Typically, an acetylene gas torch is used for preheating. Although it may take some time to get the metal up to temperature, it’s well worth the effort to ensure a high-quality weld, even in winter.
In conclusion, cold weather can indeed impact your welding, given that welding is a thermal process. However, by staying aware of the issues we’ve discussed today, using high-quality workpieces, and sourcing your welding gas from reputable bottled gas suppliers like Sultani Gas, you can successfully weld in cold temperatures. If you’d like more information about our range of gases suitable for different types of welding, please don’t hesitate to contact us. Stay warm, stay safe, and keep those sparks flying, even in the coldest of conditions.